从木支柱到智能支护:煤矿液压支架70年技术突围史
当人们谈论中国煤炭工业的崛起时,液压支架的进化史堪称一部浓缩的技术突围史诗。从建国初期木支柱的吱呀作响,到如今智能支架的毫米级精准控制,这项关乎矿工生命的技术革命,见证了中国制造从跟跑到领跑的蜕变历程。
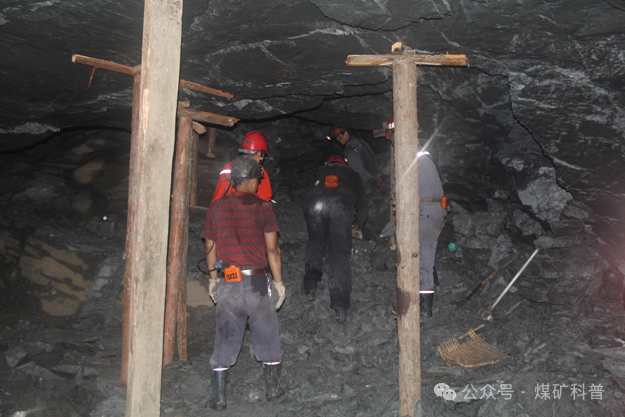
一、破冰年代:从零起步的艰难探索(1960-1980)
1964年太原分院与郑州煤机厂联合研制的70型迈步式自移支架,叩开了国产化的大门。这个重达30吨的钢铁巨人,虽然移架速度需要20秒以上,却标志着中国告别了木支护时代。当时的技术人员面临双重困境:既要攻克高强度钢板焊接工艺,又要解决液压胶管耐压难题,甚至需要自行研制专用润滑油。1973年北京煤机厂生产的BZZ垛式支架在阳泉矿务局首次应用,揭开了综采装备国产化的序幕。这个阶段的支架工作阻力仅2000kN,寿命试验仅8000次,却为后续发展积累了宝贵经验。正如王国法院士所言:”这些早期支架就像蹒跚学步的婴儿,虽然步履维艰,却走出了自主创新的第一步”。

二、技术跃迁:引进消化中的创新突破(1980-2000)
1984年沈阳蒲河矿的工业试验,见证了我国首套放顶煤支架的诞生。此时德国赫姆夏特公司的G550-22/60支架已实现6秒/架的移架速度,而我国ZY35支架仍需15秒。这个时期的技术突破体现在:架型革新:QY系列经济型支架重量仅6吨却实现3000kN工作阻力,但相比澳大利亚尤兰矿7640kN工作阻力的两柱支架仍有差距。控制升级:ZC片阀系统将乳化液流量提升至200L/min,仅为德国Panzeramtic系统500L/min的40%。材料突破:600MPa级高强度钢板抗冲击性能提升40%,但德国已普及800-1000MPa级材料。1995年郑州煤机厂研制的ZY35支架在淮南矿区创下月产30万吨纪录,而同期澳大利亚尤兰矿采用电液控制支架已实现单日3.41万吨产能。此时国产支架立柱缸径突破320mm,但德国支架立柱缸径普遍超过400mm。
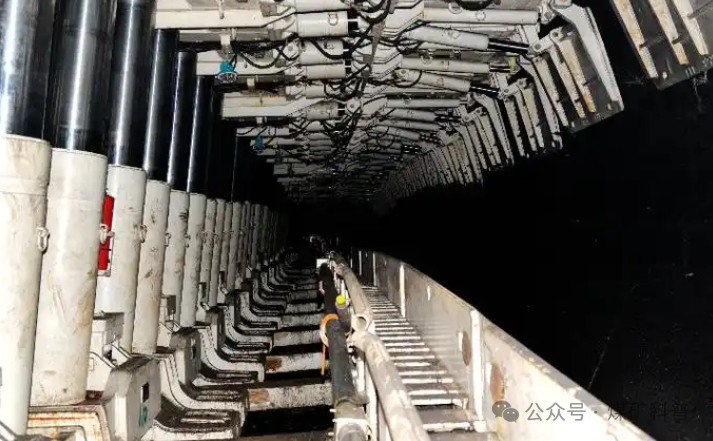
三、智造时代:从跟跑到领跑的技术超越(2000-2020)2012年郑煤机研制的8.8米超大采高支架在神东矿区投用,创造了世界支护高度新纪录。这背后是三大技术突破:材料革命:900MPa级钢板焊接工艺攻克冷裂纹难题,逼近德国Dillinger公司1200MPa级材料水平。智能控制:SAC型电液系统实现0.1秒级响应精度,而美国久益(JOY)同类系统仍保持0.08秒领先。结构创新:反四连杆设计使支护强度提升50%,结构效率超越德国DBT公司传统设计。2020年国家八部委联合发布的智能化发展指导意见,催生了新一代智能支架:
- 数字油缸配备0.01mm级位移传感器,精度达到德国海瑞克同等水平。
- 红外感知系统实现煤岩界面自动识别,较波兰Famur公司系统识别率提升12%。
- 5G通信模块支持远程集控,时延指标优于卡特彼勒4G系统40%。
在陕煤柠条塔煤矿,30种煤矿机器人组成的”钢铁战队”,让工作面作业人员从15人减至3人,达到澳大利亚必和必拓智能矿山同等水平。

四、未来图景:智能生态与极限挑战
当前液压支架正经历第四次技术革命:材料极限:1200MPa级钢板开始应用,支架寿命突破5万次循环,接近德国蒂森克虏伯实验室数据。智能进化:数字孪生系统实现超前支护决策,算法响应速度较美国久益系统快0.3秒。绿色转型:永磁直驱技术使能耗降低30%,能效比超越瑞典山特维克同类产品15%。在新疆准东煤田,世界首套10米采高智能支架正在挑战地质极限。这些配备振动能量回收装置的”钢铁巨人”,每套每年可节电50万度,较德国Eickhoff公司方案多回收12%能量。从木支柱到智能支护,液压支架的进化史印证着一个真理:核心技术买不来,唯有自主创新才能突破封锁。当新一代矿工在5G集控中心轻点鼠标时,他们操控的不仅是钢铁支架,更是一个民族七十年的技术积淀与创新雄心。
文章来源:煤炭科普公众号